In-House Powder Coat Paint Process
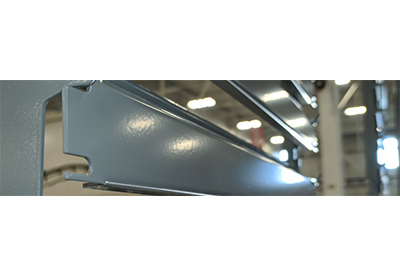
April 28, 2021
Hammond Manufacturing uses a four step process for painting their enclosures, enclosure racks and rack mounts, which includes a four-stage pre-wash, bakes within specialized ovens for metal sheets, and application of a powder coat, all of which together reduces material waste by a significant amount according to Hammond.
Process Step # 1: Four (4)-Stage Pre-Wash
Alkaline Cleaner
Cleans steel surfaces of anti-corrosion oils, added by the steel producer.
De-Ionized Water Rinse
Lower levels of dissolved solids makes the water a better solvent to wash away remaining residue and alkaline cleaner.
Nano-Ceramic Conversion Coating
Helps with paint adhesion and corrosion protection while reducing the environmental impact.
De-Ionized Water (Halo Rinse)
Like the streak-free rinse in a car wash, the halo rinse is the final rinse to remove any remaining contaminants from previous stages.
Process Step #2: Dry-Off Oven
Hammond Manufacturing’s dry-off oven ensures parts are dry prior to the powder coat application. If water is present during powder application, water marks and imperfections will appear in the paint finish.
Process Step #3: Electrostatic Powder-Coat Application
Electrostatic powder-coat is achieved by applying an electrostatic charge to the powder particles which are attracted to a grounded part. Spray guns are used to apply the paint using both automatic and manual techniques.
Process Step #4: Powder Coat Bake Oven
Hammond Manufacturing’s bake oven cures the powder into a seamless coating. The bake oven consists of a 33ft infra-red oven booster that brings the part up to the required cure temperature. The remaining 179ft is a convection bake oven that maintains a steady baking temperature of 400 degrees.
More About the Powder Coat Process
Is the Finish Rust-Proof?
When applied to mild steel and installed in a non-corrosive environment, the powder coat paint process holds up better than wet paint. UL/CSA Type 4 products are subjected to a 600 hour salt spray test.
The Nano-ceramic coating applied during the wash process helps with corrosion protection. In addition, a fully painted product resists external elements from corroding the base material.
Powder coated products are more resistant to diminished coating quality from impacts, moisture, chemicals, ultraviolet light and extreme weather conditions.
What is the Powder?
The main ingredient of the powder is a polymer resin in addition to curing agents, pigments, leveling agents, flow modifiers, and other additives.
During the baking process the polymer resin powder melts coating the sheet metal and binds the polymer into a tighter and denser finish.
Powder coating provides a more durable and longer lasting finish compared to conventional wet painting. Also, powder coating is typically a one-coat finish.
How Durable is the Finish?
To determine how durable the paint finish is and to ensure a quality finish, Hammond completes a “cross hatch” test.
In accordance to the ASTM Standard D3359 procedure, the test is performed by scribing the paint finish in a cross hatch pattern followed by applying a pressure sensitive tape and pulling the tape from the surface. The cross hatch grid pattern is examined with a magnify glass to determine the paint adhesion.
A pass is determined if the edges of the cuts are completely smooth; none of the squares of the grid pattern are detached.
Environmental Benefits
Paint Reclaim
Every year, Hammond reclaims 85% of paint used. Our paint process includes the ability to re-use (reclaim) paint that misses the product in the paint booth. This process keeps 146,200 kg of waste paint from ending up in landfill.
Water Treatment
Approximately 98% of water used in our paint process is recovered and reused. The remaining 2% is treated in-house to exceed municipal standards.
No Chemical Exposure
Unlike wet spray-painting environments, our powder coat paint process does not off-gas any fumes or chemical exposure making it ideal for education, healthcare and office applications.