NEMA vs IP Ratings: How Much Ingress Protection Do I Need?
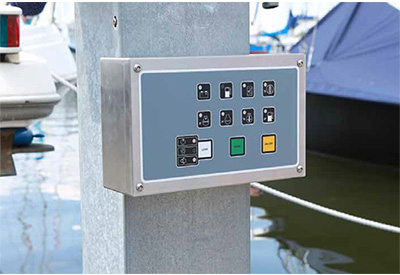
October 19, 2021
COMPARING THE TWO SYSTEMS
NEMA and IP ratings both measure the same thing: an enclosure’s ability to withstand the ingress of dust or water. This matters because watertightness is not a binary concept: housings are not simply waterproof/not waterproof.
Varying degrees of pressure play a huge part in how well your enclosures will cope with exposure to water or dust. A splashproof enclosure will not resist prolonged immersion. And a fully submersible enclosure may not cope with high-pressure water jets.
So it’s crucial to specify the correct NEMA or IP rating for your industrial electronic enclosures. But this can be confusing because the two systems use different variables. And the numerical ratings do not correlate in the way you’d expect.
Here are some examples:
- – NEMA 4 and 4X are similar to IP 66 – but NEMA 5 is similar to IP 52
- – NEMA 6 and 6P are like IP 67 – but NEMA 12 and 12 K are again closer to IP 52.
Yes, it is possible to compare and cross-reference ratings – but it’s crucial to specify your ingress protection requirements as accurately as possible. And for this you’ll need to examine the two rating systems in detail…
WHAT IS THE NEMA SYSTEM? HOW DOES IT WORK?
NEMA is the US system for measuring ingress protection. It was developed by the National Electrical Manufacturers Association, which represents around 325 electrical equipment and imaging manufacturers.
Ingress protection is judged according to 13 NEMA types, some of which include multiple classifications. This gives 21 different ratings. Importantly – a high number does not necessarily indicate a high level of watertightness: it shows the correct level of protection required for a particular application.
NEMA INGRESS PROTECTION RATINGS
NEMA Types 1, 2, 5, 12 and 13 are for indoor applications. They are not recommended for outdoor use. Types 7, 8 and 9 are for hazardous environments in sectors such as mining, oil/gas and chemicals.
- 1. General-purpose. Protects against falling dust, light and indirect splashing but is not dust-tight. Used indoors and under normal atmospheric conditions. Prevents employees or objects from accidentally touching hazardous components.
- 2. Drip-tight. Similar to Type 1 but with the addition of drip shields. Used where condensation may be severe (as in cooling and laundry rooms).
- 3. Weather-resistant. Protects against falling dirt and windblown dust, against weather hazards such as rain, sleet and snow. Is undamaged by the formation of ice. Used outdoors on ship docks, in construction work and in tunnels and subways.
- 3R – as 3, but omits protection against windblown dust.
- 3S – as 3, but also operable when laden with ice.
- 3X, 3RX, 3SX – X indicates additional corrosion protection. Commonly used near salt water.
- 4 and 4X. Watertight. Must exclude at least 65 gallons of water per minute from a 1” nozzle delivered from a distance not less than 10ft for five minutes. Used outdoors on ship docks, in dairies, in wastewater treatment plants and breweries. X indicates additional corrosion resistance.
- 5. Dust-tight. Provided with gaskets or equivalent to exclude dust. Used in steel mills and cement plants.
- 6 and 6P. Submersible. The design depends on specified conditions of pressure and time. The enclosures can be submersible in water or oil. Used in quarries, mines, and manholes. Type 6 is temporarily submersible; 6P withstands occasional prolonged submersion. Neither is intended for continuous immersion.
- 7. Certified and labelled for use in areas with specific hazardous conditions – for indoor use in Class I, Groups A, B, C, and D environments as defined in National Fire Protection Association (NFPA) standards such as the National Electrical Code (NEC) NFPA 70.
- 8. Certified and labeled for use in areas with specific hazardous conditions: for indoor and outdoor use in locations classified as Class I, Groups A, B, C, and D as defined in NFPA standards such as the NEC NFPA 70.
- 9. Certified and labeled for use in areas with specific hazardous conditions: for indoor and outdoor use in locations classified as Class II, Groups E, F, or G as defined in NFPA standards such as the NEC NFPA 70.
- 10. MSHA. Meets the requirements of the Mine Safety and Health Administration, 30 CFR Part 18 (1978).
- 11. General purpose. Protects against the corrosive effects of liquids and gases. Meets drip and corrosion-resistance tests.
- 12 and 12K. General purpose. Intended for indoor use, provides some protection against dust, falling dirt and dripping non-corrosive liquids. These enclosures offer some protection against access to hazardous parts. They meet drip, dust and rust-resistance tests. 12K enclosures are manufactured with knockouts.
- 13. General purpose. Primarily used to provide protection against dust, spraying of water and non-corrosive coolants. Meets oil-exclusion and rust-resistance tests.
HOW DO IP RATINGS WORK?
IP ratings are the international standard for ingress protection. They are defined in IEC standard 60529 and published by the International Electrotechnical Commission. The equivalent European standard is EN 60529.
THE IEC SYSTEM IS BASED ON TWO DIGITS…
The first IP digit defines protection against dust ingress – the higher the number, the better.
- X = no data available to specify a protection rating.
- 0 = Not protected.
- 1 = Large foreign bodies. Protection against accidental large surface (ie, hand) contact with live and internal moving parts. However, there is no protection against intentional access to these parts. Protection against the penetration of solid foreign bodies with a diameter greater than 50 mm.
- 2 = Medium-sized foreign bodies. Protection against contact between the fingers and live or internal moving parts. Protection against the penetration of solid foreign bodies with a diameter greater than 12 mm.
- 3 = Small foreign bodies. Protection against contact between live or internal moving parts and objects. Protection against the penetration of solid foreign bodies with a diameter greater than 2.5 mm.
- 4 = Granular foreign bodies. Protection against contact between live or internal moving parts and objects with a thickness of more than 1 mm.
- 5 = Dust deposits. Complete protection against contact with live or internal moving parts. Protection against harmful dust deposits. The penetration of dust is not fully prevented – but dust will not penetrate in sufficient quantities to affect the functionality.
- 6 = Dust ingress. Complete protection against contact with live or moving internal parts. Protection against the ingress of dust.
The second digit defines protection from ingress of water. Again, the higher number generally indicates better protection but – like the NEMA system – the numbers are application-specific. For instance, IP 67 and IP 68 protect against immersion in water. But they are not suitable for applications involving high-pressure jet washing, which calls for IP 69K protection.
- X = no data available to specify a protection rating.
- 0 = Not protected.
- 1 = Protected against water droplets. Vertically falling droplets must not have any damaging effects. Test: water equivalent to 1 mm of rainfall per minute for 10 minutes.
- 2 = Protected against water droplets if the enclosure is inclined up to 15°. Vertically falling droplets must not have any damaging effects if the enclosure is inclined up to an angle of 15° either side of vertical. Test: four positions are tested within two axes, water equivalent to 3 mm rainfall for 10 minutes (2.5 minutes for each direction of tilt).
- 3 = Protected against water spray. Water sprayed at an angle of up to 60° either side of vertical must not have any damaging effects. Test: water is sprayed at a pressure of 50-120 kPa, 10 litres/minute, one minute per square metre for at least five minutes. This test is repeated with the enclosure rotated 90°.
- 4 = Protected against splashing water. Water that is splashed against the enclosure from any direction must not have any damaging effects. Test duration: 10 minutes.
- 5 = Protected against water jets. Water that is sprayed in a jet against the enclosure from any direction must not have any damaging effects. Test: 12.5 litres/minute of water is sprayed at 30 kPa from a distance of three metres – one minute per square metre for at least three minutes.
- 6 = Protection against powerful water jets. Water sprayed in a powerful jet against the enclosure from any direction must not have any damaging effects. Test: 100 litres/minute of water is sprayed at 100 kPa from a distance of three metres – one minute per square metre for at least three minutes.
- 6K = Protection against powerful water jets with increased pressure. Water sprayed against the enclosure from a powerful jet (under elevated pressure and from any direction) will have no harmful effects. This rating is found in DIN 40050, not IEC 60529. Test: 75 litres per minute at 1,000 kPa at a distance of three metres for at least three minutes.
- 7 = Protection against the effects of temporary submersion in water. Water must not seep into the enclosure in any quantity that could cause damage when the enclosure is submerged underwater temporarily. Test: immersion in water for 30 minutes to a depth of one metre (at the lowest point of the enclosure) or with the highest point 150 mm below the surface, whichever is deeper.
- 8 = Protection against the effects of long-term submersion. Water must not seep into the enclosure in any quantity that may have damaging effects when the enclosure is submerged in water (usually up to three metres deep) on a long-term basis under conditions agreed between the manufacturer and user. These conditions must be harsher than those for code 7.
- 9K = Protection during high pressure/steam spray cleaning. Water sprayed against the enclosure in a powerful, high-pressure jet (from any direction) must not have any damaging effects. Test: 14-16 litres of water (at 80°C) is sprayed at 8-10 MPa at a distance of 0.1-0.15 metres for 30 seconds at each of four angles (two minutes in total).
It is important to note that the IP ratings system covers only ingress protection from dust and water. Unlike the NEMA system, it makes no reference to corrosion resistance.
IMPORTANT NEMA RATINGS AND THEIR NEAREST IP EQUIVALENTS
NEMA 4/4X vs IP 66. Both offer complete protection against dust. NEMA 4 is sleet resistant, making the enclosures suitable for both indoor and outdoor use. NEMA 4X offers additional corrosion resistance. IP 66 enclosures provide protection against powerful water jets (but not against high-pressure jets or steam cleaning – for which IP 69K is needed). View ROLEC’s wide range of IP 66 enclosures >>.
NEMA 6/6P vs IP 67. Again, both offer complete protection against dust. NEMA 6 enclosures are watertight and can be submerged occasionally; NEMA 6P housings can be submerged for longer. IP 67 enclosures protect against immersion at depths between 150 mm and 1,000 mm. View ROLEC’s IP 67 enclosures >>.
NEMA vs IP 69K. Sadly, there is no direct NEMA equivalent of IP 69K. If your application involves repeated high-pressure jet washing and steam cleaning then we strongly recommend that you specify diecast aluminum or stainless steel IP 69K enclosures. View the IP 69K rated ROLEC enclosures >>.
Important note: This cross reference is provided as a guide only
NEMA and IP ratings are not equivalent, the methods used to test the enclosures are not the same. It is important to note that while NEMA standards will meet or exceed IEC 60529 IP ratings, it does not work the other way round. IP ratings cannot be used to comply with a specific NEMA classification. To ensure compliance, electronics equipment should be tested to the required standard once all the equipment is fitted into the housing.
https://www.rolec-usa.com/en/news/blg2109-nema-vs-ip-ratings/