A Condensed Guide to Automation Control System Specification, Design and Installation – Parts 1 & 2
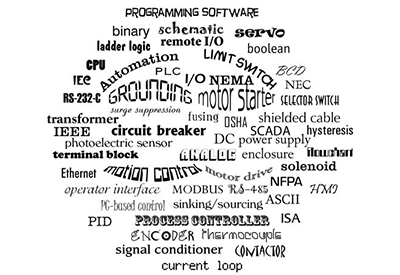
January 4, 2022
By Tom Elavsky, Owner, AutomationDirect
The following is Part 1 and 2 of a four-part series of articles on Control System Design that can act as a general guide to the specification, design and installation of automated control systems. The information and references are presented in a logical order that will take you from the skills required to recognize an operation or process suited for automating, to tips on setting up a program, to maintaining the control system. Whether you are an expert or a novice at electrical control devices and systems, the information presented should give you a check list to use in the steps to implementing an automated control system.
Electrical control systems are used on everything from simple pump controls to car washes, to complex chemical processing plants. Automation of machine tools, material handling/conveyor systems, mixing processes, assembly machines, metal processing, textile processing and more has increased productivity and reliability in all areas of manufacturing, utilities and material processing.
You may have come to realize that an operation or process used to produce your end product is very laborious, time consuming, and produces inconsistent results. You may have also visualized ways that would allow you to automate the operation. Automating the process will reduce the amount of manual labor, improve throughput and produce consistent results. You may have the skills to develop the mechanical means and select the appropriate equipment to make this happen, and although you have a basic understanding of electrical control devices, you may not have the experience to put it all together. Your first option may be to enlist the help of a qualified System Integrator. If you do decide to use a System Integrator, it would be beneficial to understand as much as possible about automation control system devices and their terminology so that your communications with the System Integrator go faster and more smoothly.
In most cases, special expertise is required to design and install industrial automation control systems. Persons without such expertise or guidance should not design and install automation control systems because they can fail and cause serious injury to personnel or damage to equipment. The information provided in this whitepaper is provided “as is” without a guarantee of any kind. We do not guarantee that the information is suitable for your particular application, nor do we assume any responsibility for its use in your application.
It is our intent to produce this whitepaper as a usable guide, with additional information, including a typical “real world” application that can be followed from concept to completion. It is not our intent for the guide to cover every possible topic dealing with automation control systems or to even suggest that the topics being covered are fully detailed. Instead, the topics are aimed at giving the reader a good starting reference for automated control systems.
In Part 1, we will cover the topics of Safety and Identifying an operation or process that could benefit from automation. We will then cover control device specification, control system design and construction, control system installation, and finally control system maintenance. The topics will be broken down as follows:
- • Part 1 – SAFETY and IDENTIFICATION
- • Part 2 – SPECIFICATION
- • Part 3 – DESIGN and BUILD
- • Part 4 – INSTALL and MAINTAIN
Part 1: System Identification and Safety
The first and most important item to consider before attempting an automated control system, or even a simple on/off control for a pump, is safety, both for personnel who may be working with or near the automated equipment, as well as to prevent damage to the equipment.
To minimize the risk of potential safety problems, you should follow all applicable local, state and national codes that regulate the installation and operation of your control system, along with the equipment or process it is designed to control. These codes vary by area and usually change over time. It will be your responsibility to determine which codes should be followed and to verify that the equipment, installation, and operation is in compliance with the latest revision of these codes.
Most likely your control system will be dealing with electrical energy, so your first goal will be to eliminate the risk of fire and electrical shock to personnel. The top organizations that provide applicable standards and codes are referenced below, but even before you get to this area of safety, it would be wise to educate yourself as much as possible about electricity and electrical equipment in general. A good understanding of basic electricity, including DC and AC theory and practice, Ohm’s Law, etc. will go a long way in helping you understand the various codes and standards. There are many good publications and articles on the subject of basic electricity and some local technical colleges offer courses covering subjects dealing with basic electricity. Some even offer courses in Programmable Logic Controllers (PLCs), which can be very useful when dealing with automated control systems. Also, many Web sites offer free tutorials covering basic electricity and PLCs. It would be beneficial to have some understanding of electronic devices, such as the operation of a transistor and other solid state devices, as well as understanding of the use and operation of electrical test and measurement instruments, such as voltmeters, current loop meters, clamp-on amp meters, etc.
At a minimum, you should follow all applicable sections of the National Fire Protection Association (NFPA) fire code, and the codes of the National Electrical Manufacturer’s Association (NEMA). There may also be local regulatory or government offices that can help determine which codes and standards are necessary for the safe installation and operation of electrical control equipment and systems.
Another area of safety that needs to be considered for automated control systems is lockout/tagout procedures as specified by Occupational Safety and Health Administration (OSHA). “Lockout/tagout” refers to specific practices and procedures to safeguard operators and maintenance personnel from the unexpected energization or startup of machinery and equipment, or the release of hazardous energy during service or maintenance activities. In order to have your control system make use of a lockout/ tagout procedure, the design should include the ability to shut off, neutralize, or isolate any energy source, such as the main electrical feed, but also any pneumatic, hydraulic or mechanical energy storage device. The means to do this should be considered in the initial design of the automated control system. Additional information can be found on OSHA’s Web site at: www.osha.gov/SLTC/controlhazardousenergy/.
There are many reasons why the electrical devices that you will use in the design of your automated control system should be listed, approved or registered with a testing laboratory. One reason is to ensure that the device meets standards that will prevent failure that could lead to catastrophic results. Another reason might be for insurance or compliance purposes. One of the most specified and premier safety testing laboratories is Underwriters Laboratories (UL). One of the most applicable areas of interest for control systems is UL’s Standard for Safety 508A. If your control system panel requires being built to UL508A, then you will need to contract directly with UL to become a UL508A panel builder or use an existing UL508A panel builder. Additional information can be found at: https://standardscatalog.ul.com/standards/en/standard_508a.
Compliance to UL508A for AutomationDirect products can be found on our Web site at: http://support.automationdirect.com/compliance.html.
The following are other safety points to consider in the design of your automated control system:
- – Emergency Stop – The control system must provide a quick manual method of disconnecting all system power to the machinery, equipment or process. The disconnect device or switch must be clearly labeled “Emergency Stop”. After an Emergency shutdown or any other type of power interruption, there may be requirements that must be met before the control system or PLC control program can be restarted. For example, there may be specific register values in the PLC memory that must be established (or maintained from the state prior to the shutdown) before operations can resume. There may also be mechanical positions of equipment that have to be moved or jogged to the proper position.
- – Accidental Powering of Outputs – Do not rely on the automation control system alone to provide a safe operating environment. You should use external electromechanical devices, such as relays or limit switches, that are independent of any electronic controlling devices, such as a solid state relay or a PLC output module, to provide protection for any part of the system that may cause personal injury or damage. These devices should be installed in a manner that prevents any machine operations from occurring unexpectedly. For example, if the machine has a jammed part, the controlling system or PLC program can turn off the motor rotating a saw blade. However, since the operator must open a guard to remove the part, you should also include a bypass switch that disconnects all system power any time the guard is opened.
- – Orderly Equipment Shutdown – Whether using a control system designed around relays and timers or a PLC, an orderly system shutdown sequence should be included in your design. If a fault is detected, then any mechanical motion, valve position, etc., needs to be returned to its fail-safe position and the equipment/process stopped. These types of problems are usually things such as jammed parts, broken cutting tools, bin full, etc. that do not pose a risk of personal injury or equipment damage. If a detected problem would result in risk of personal injury or equipment damage, then use other means to deal with it, such as applying a brake to rotating equipment to stop it before personnel can come in contact with it.
- – Grounding – To prevent electrical shock, incorporate good grounding practices in the design, construction and installation of your system. Use protective devices for faulted conductors to prevent fire, and also realize that good grounding practices can reduce electromagnetic and radiated noise interference to sensitive electronic devices.
- – Control Power Distribution – Develop a power distribution scheme in the control system circuitry, according to code, that ensures all circuits are protected with fusing, circuit breakers or other interrupting means coordinated such that only the faulted circuit will be opened (de-energized), allowing other powered equipment and devices to continue to operate.
- – Unauthorized Access – Make sure all enclosures and cabinets that have energized circuits are secured to prevent unauthorized personnel from gaining access without the proper tool, key or other authorized means.
- – Finger-Safe and Dead Fronts – Another safety area to consider is the use of devices that have finger-safe terminal connections, which are surrounded by insulated guarding. The use of protective guards over live circuits should also be considered, even on control panels that have limited access, so it is safer for maintenance electricians and authorized personnel to troubleshoot or make adjustments to electrical control devices. Dead fronts should be used on control system enclosures where the operator needs to make adjustments to devices, such as selector switches, thumbwheels, potentiometers, etc., and the controls need to be inside the enclosure so as to protect them from outside weather conditions. The dead front is normally an interior door that is mounted in front of the main control panel. The outside enclosure door may still require key entry by the operator, but the dead front interior door with adjustable devices is interlocked so that it requires a switch to open it, disconnecting power to the electrical devices mounted on the main control panel.
- – Closed-loop Control – It is your responsibility in any type of closed-loop control system to ensure that if the feedback signal is lost, the system shuts down so as not to cause injury to personnel or damage to the equipment.
Identifying Process for Automation
The first step in configuring an automated control system is to identify what can be automated. You need to have a good understanding of basic electricity and safety.
It is also important that you have an understanding of basic hydraulics, pneumatics, mechanical operating mechanisms, electronics, control sequences, etc. and a solid knowledge of the operation or process that you are going to automate.
You should understand how to control motion and movement, regulate the flow of fluids, dispense granular materials, orient parts, sense product in position, detect when an operation is complete, etc. As a simple example, let’s say we have a conveyor that moves our product from point A to point B. The conveyor is powered by a 3-phase AC motor, which is turned off and on by a manually controlled motor starter and includes, for fire protection, both short circuit and overload protection. The system requires an operator standing at the motor starter to watch as the product reaches the entrance to the conveyor, and to turn the conveyor on to move the product. The operator must also turn the conveyor off once the product has reached the discharge end.
To automate the conveyor, we will need to replace the manually controlled motor starter with an electrically controlled motor starter, including short circuit and overload protection. We will need to size the motor starter to work with the existing conveyor motor. (Refer to our Web site at: http://www.automationdirect.com/static/specs/fujimcselection.pdf for information on specifying and sizing motor starters.)
We will also need to identify where to locate sensors such as limit switches, photoelectric sensors, proximity sensors, etc. that will indicate when an operation is completed. This is required so our control system knows when to proceed to the next step in our operation. As an example, we usually need a limit switch to detect when a cylinder is fully extended, as in the case when the cylinder is used to push our product onto a conveyor. The cylinder “fully extended” signal is used to de-energize the solenoid valve that provided the air pressure to the pneumatic cylinder. We also need a limit switch to indicate when the cylinder has fully retracted, and provide a signal to the start/stop control of the conveyor that the product push cylinder is out of the way for the next product. Another application for a sensor is to indicate when the product has reached the conveyor. The sensor can be a limit switch with a roller arm that comes in contact with the product or a photoelectric sensor that can detect the product by using an infrared beam of light. The photoelectric approach may be the better choice because the position of the product on the conveyor belt may vary. (Refer to our Web site at: www.automationdirect.com/static/specs/peselection.pdf for information on selecting photoelectric sensors.)
We would continue with this analysis, looking at each piece of equipment or component in our system, and select a device that could control or sense it. Some examples include an electrical solenoid valve to control water used to wash residue from a product, or a pneumatic valve to control air pressure to a cylinder operating a gate that diverts product on a conveyor, or energizing a control relay to signal that a product is in position on a scale.
In some instances we may need to vary the speed, rate or position of our controlling device, such as varying the speed of a conveyor, changing the amount a valve opens to control a flow rate, or remotely changing the set-point level for a tank. This could be accomplished by using an analog output signal. An analog output signal is a varying signal that corresponds to the real value we have determined and calibrated into the device. For example, a 0 to 10 VDC signal could represent a conveyor speed of 0 to 500 feet per minute. An analog signal to the speed controlling device for the conveyor motor of 5 VDC would result in a conveyor speed of 250 feet per minute.
Identifying devices to control motion, flow, events, etc. and sensing completion is basically identifying the I/O (inputs and outputs) of our control system. Once these devices are identified, they can be used as the field devices in a PLC-based system, or they can be “hard-wired” for simpler applications.
You will also want to determine if your automated control system will benefit from the use of an operator interface, also referred to as a Human Machine Interface (HMI). If your process requires making changes to set-point values, process time, flow rates, etc., then the use of an HMI is the best way to proceed. In these situations, you will most likely need a PLC that can easily communicate with the HMI device.
If your application requires keeping data records for reference, traceability, history, trending, meeting regulations, etc., then you should look at using a control system that would fall into the category of a “Supervisory Control And Data Acquisition” (SCADA) system. Most of these control systems would be comprised of PLC-type I/O that interface to a PC with appropriate software.
References:
For information on PLCs and PLC programming fundamentals visit: www.interconnectingautomation.com.
You may also want to visit the AutomationDirect Customer Forums at: https://forum.automationdirect.com or watch our tutorial videos at www.automationdirectcom/videos
Information for the National Electrical Manufacturer’s Association (NEMA) can be found at their Web site at: www.nema.org.
Further information for the National Fire Protection Association (NFPA) can be found at their Web site at: www.nfpa.org. Some of the more useful publications are the National Electrical Code (NEC), publication NFPA 70 and also as a good reference refer to the Electrical Standard for Industrial Machinery, publication NFPA 79.
Part 2: Control Device Specification
In Part 1 of Control System Design, we covered safety aspects involved in the use of automated control systems and discussed some tips used in identifying which manufacturing equipment and processes can be automated.
In Part 2, we will cover how to specify the various devices required for controlling the equipment in an automated system. Your specifications need to include not only the “controlling” devices for your application, but also items such as the housing or enclosure for the devices, the type of wire required to meet the various codes, agency approvals required for safety and insurance purposes, environmental conditions, etc.
The first skill we need to develop in this effort will be the gathering of all the equipment parameters and specifications needed to specify the devices required to control the equipment. We need to be the proverbial detective who would ask questions such as;
- • What is the operating voltage?
- • What is the power rating?
- • How much current does it draw?
- • What is the operating temperature range?
- • What is the relative humidity range?
- • What are the mounting dimensions?
- • What are the minimum mounting clearances?
- • What is the duty cycle?
- • How will the system be used?
- • Who will be using the control system?
Control System Devices
The devices you need to specify in your control system will generally fall into one of three categories; input devices, output devices and the processing unit.
Input Devices
Input devices are used to sense a condition, detect movement or position, indicate a limit or set point has been reached, sense intervention by an operator, detect an alarm, etc. Typical input devices may include limit switches, photoelectric sensors, pushbuttons, proximity sensors, an operator interface, etc. These input signals are generally in an ON or OFF state. We can look at an input from a device, such as a photoelectric sensor used to detect an obstruction, and state that when the sensor sees the obstruction, the sensor is ON; in other words we have a true condition.
When the sensor is not obstructed, then the input is OFF; or we can say the condition is false. These types of signals are called discrete signals, meaning they are always one of two states; ON or OFF. They can be wired into a PLC input module and the PLC can be programmed to use the status of the signals to execute the logic to control the automated system. Or these same signals can be used in a “relay logic” system, where control relays are hardwired to create the system logic.
Of importance to our specifications are the ratings of these input devices:
- • What is the operating voltage; 24, 120 or 240 Volt AC or DC?
- • If they are rated for DC, are they sinking or sourcing?
- • What distances can they sense?
- • How much force can be applied to the actuator?
- • How much current do they require?
As a note, most PLC DC input modules can be configured as sinking or sourcing.(1)
Also keep in mind that when selecting a sensor device, such as to detect the presence of product or sense the end of travel for a mechanism, it is very important to consider the environment in which the sensor will operate. This should not only include temperature and humidity ranges, but in some cases, indoor or outdoor use, altitude, ability for the sensor to be washed down, etc. Photoelectric sensors are sensitive to the atmosphere in which they can efficiently work. If there is a lot of dust, dirt and/or mist in the air, then the optics can easily become dirty or coated, reducing their sensitivity and operating distance.
Output Devices
Output devices are used to control actions such as motion, start/stop of equipment like conveyors and pumps, on/off control of valves, operator alerts/prompts, status indications, etc. Typical output devices include relays, motor starters, pilot lights, operator interface graphics and numeric display, etc. These output signals, like input signals, are also discrete; either ON or OFF. The signals can be wired from a PLC output module to control the devices, such as starting and stopping motors, energizing a valve to control water flow, illuminating a pilot light to alert an operator to a condition such as “Bin Full”, etc. Output signals can also be wired directly to a controlling device using hardwired relay logic.
Of importance to our specifications are the ratings of these output devices:
- • What is the operating voltage; 24, 120 or 240 Volt AC or DC?
- • If they are rated for DC, are they sinking or sourcing?
- • What is the current draw?
- • What is the duty cycle?
- • What is the operating temperature range?
- • What are the mounting dimensions?
For example, if our process uses a solenoid valve to control water flow to a wash station, we would need to know the operating voltage of the valve and how much current it draws. We also need to know not only the on-state current draw of a valve, but also the inrush current, so that we can properly specify a PLC output module or a control relay. Although a valve may be rated to draw 250 mA continuous current, it may have an inrush of 800 mA when first energized. If an output module has eight output points and each point is rated for 1 amp continuous duty, after thermal considerations, the entire output module has a total rating of 6 amps and therefore has a common fuse rated at 6 amps. If we had solenoid valves connected to all eight output points and our program called for them all to energize at the same time, the total inrush current would be 8 times 800mA or 6.4 amps, and most likely would blow the fuse. The solution could be to select an output module with a higher current rating or to use the ladder program to sequence the valves, preventing them all from being energized at the same time. Another option is to split up the valves between several output modules, using the remaining points to power smaller loads such as pilot lights. Certain output types may have derating curves depending on the ambient temperature and the number of outputs energized. Keep in mind that DC output modules can be sinking or sourcing type.
The processing unit
All control systems can typically be defined as having inputs, outputs and some form of decision making going on in between so that the outputs are controlled based on the status of the inputs. This brings us to our third category, the “decision making” element. This element can be performed by a PLC, where we have inputs, outputs and a central processing unit (CPU) that uses logical programming to make decisions based on input status and the logical conditions set in the program (see figure 3).
A similar device that can be looked at in the same manner is a personal computer (PC). The keyboard, mouse, scanner, etc. would serve as input devices and the monitor, printer, speakers, etc. would be the output devices. The microprocessor used on the motherboard, along with its memory, the operating system, and the application program would serve as the decision making element. As a matter of fact, PCs are used in some automated control systems as the decision making element, together with industrial input and output (I/O) modules. These PC-based systems rely on the communication ports or Ethernet connections to monitor and control the I/O. The application software typically allows a programmer to develop a graphical interface that gives an operator interaction with the equipment or process. With some research and experience, you will learn how to determine how much “decision making” ability your control system requires. Cost restraints may require you to compare implementing the control system with either a PLC, PC-based control, or simple hardwired relay logic. But don’t forget the fact that a PLC or PC-based control system allows easier changes and future expansion.(2)
Other device types
Another area of inputs and outputs involves the use of analog signals in a control system. Analog signals are variable and can represent a range of values. As a quick example, we may want to monitor the level of a liquid in a tank that is 100 feet tall. We can use a sensor that will produce a signal that is represented by a voltage range of 0 to 10 volts DC, with 0 feet being equal to 0 VDC and 100 feet being equal to 10 VDC. Analog signals are typically linear, so a 5 VDC signal would tell us the tank level is at 50 feet. The analog signal could be wired into a PLC analog input module, and in the ladder program we could compare the actual level to a set point and produce a discrete signal that would cause an output point to start a pump to raise or lower the level.
Inductive devices
When selecting a device to control a prime mover, such as an industrial motor to power a conveyor, or a valve to control a hydraulic cylinder, you will need to determine the ratings of the equipment:
- • What is the operating voltage?
- • What is the maximum current draw?
- • What type of environment is it being used in?
An industrial induction motor may have ratings such as 230/460 VAC, 3-phase, 1725 RPM, a FLA (full load ampere) of 10.5 amps at 460 VAC, etc. This information can be obtained from the manufacturer’s catalog, or website, or directly from the motor nameplate. In the case of a motor, you will need the ratings to choose the motor starter or possibly a variable frequency drive for either start/stop control or speed control of the motor.
Other considerations
There are other points to consider in the specification of devices being used in your automated control system – duty cycle, surge suppression, enclosure type, heating and cooling, power, environment, static electricity and agency approvals.
Duty Cycle
When using a solenoid valve, you will want to know its operating voltage, nominal current draw and current inrush to help select the type of output device required to control its operation. It is also important to have an understanding of the solenoid valve’s duty cycle (time on vs. time off). We would not want to operate a solenoid valve rated at 50% duty cycle in a continuous mode with an on time of 10 seconds and an off time of only two seconds. The short off time would not allow for the solenoid to properly cool down.
Surge Suppression
Solenoid valves, motor starters, etc. make use of an inductive coil for their operation and the coil can produce high voltage spikes that can damage output devices and nearby electronic equipment. It is always recommended to use some form of surge suppression to eliminate these voltage spikes.
Enclosures
Selecting a proper enclosure is important to ensure safe and proper operation of your equipment. The minimum considerations for enclosures should include:
- • Conformance to electrical standards (Reference NEC)
- • Protection from the elements in an industrial environment (Reference NEMA)(3)
- • Common ground reference (Reference NEC)
- • Access to the equipment (Reference OSHA)(4)
- • Security or restricted access (Reference OSHA)
- • Sufficient space for proper installation and maintenance of equipment
Heating/Cooling
Ensure that the devices used in your control system aren’t subject to overheating, or if installed in a colder climate, the devices aren’t being used below the listed low temperature operating range. Your control system, because of its physical location, may require you to have both a cooling system, such as an A/C unit, and a small heating unit as part of the same enclosure. This will ensure the devices are always operating within their temperature specifications. Basic thermal management is not difficult for most automated control systems. Investing a little thought during the specification stage can save you a great deal of redesign down the road.
DC Power
If using DC voltage from a power supply in your control system, consider using a power supply rated for at least twice the calculated load. This should satisfy one of the requirements if you need to have your control system UL 508 approved and will allow the power supply to operate at a lower temperature, thus increasing its life.
The following table is an example of NEMA’s common environmental specifications that generally apply to automation equipment. IEC also has a list of common environmental specification designations for enclosures and equipment.
Static Electricity
Most equipment and devices will operate down to 5% relative humidity. However, static electricity problems occur much more frequently at humidity levels below 30%. Make sure you take adequate precautions when you touch the equipment. Consider using ground straps, anti-static floor coverings, etc. if you use the equipment in lowhumidity environments.
Agency Approvals
Some applications require agency approvals for particular components. Some of these required approvals are:
- • UL (Underwriters’ Laboratories, Inc.)(5)
- • CUL (Canadian Underwriters’ Laboratories, Inc.)
- • CE (European Economic Union)
The requirements for any of these agency approvals need to be part of your specification and will determine the selection of most of your controlling devices.
Enclosure Lighting and Convenience Receptacle
It is always a good idea to include interior lighting for your control system enclosure or cabinet to help during routine maintenance to the control system. Provide a convenience receptacle inside the control system enclosure to supply power to test equipment, calibration equipment, etc.
Product Selection
Suppliers’ literature and Web sites are an excellent resource for evaluating product specifications. For industrial control product selection information for AutomationDirect products, refer to https://www.automationdirect.com/adc/ProdInfo/ProdInfo
Footnotes:
- – 1 For “Sinking and Sourcing Concepts” refer to: https://library.automationdirect.com/sinking-sourcing-concepts
- – 2 For “Considerations for Choosing a PLC” refer to: http://support.automationdirect.com/docs/worksheet_guidelines.html
- – 3 Information for the National Electrical Manufacturer’s Association (NEMA) can be found at their Web site at:
http://www.nema.org. - – 4 Additional information can be found on OSHA’s Web site at: www.osha.gov/SLTC/controlhazardousenergy
- – 5 Additional UL information can be found at: http://industries.ul.com/industrial-systems-and-components

https://cdn.automationdirect.com/static/press/Control-System-Design-white-paper.pdf