Introduction to Open Platform Communication (OPC)
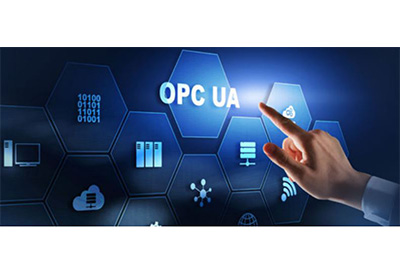
March 8, 2022
What is Open Platform Communication?
Open Platform Communications (OPC) is an interoperability standard that allows multiple manufacturers to securely exchange industrial automation data. It defines a real-time transmission protocol for managing various devices with in-plant between sensors, field devices, controllers, and applications on the shop floor, as well as between the OT and enterprise IT (Cloud) systems.
OPC is an M2M communication protocol used in the Industrial Automation Industry. When more industrial automation system components desire to communicate, it becomes feasible to collect and analyse information from each component, break down data, improve efficiency, responsiveness, and make better business decisions. OPC, which stands for Object Linking and Embedding for Process Control and is based on OLE, COM, and DCOM technology, is intended to serve as a bridge for Windows-based application and process control hardware. The OPC server converts the hardware communication protocol, as well as any software that needs to connect to the hardware becomes the OPC client. OPC Instructions are used by OPC clients and servers to identify, send, and control commands that are executed in a controller or I/O module.
OPC UA (Unified Architecture) is the OPC Foundation’s next generation standard, an update to the original OPC interoperability standard that addresses the needs and new challenges in security and data modelling while also providing a feature-rich technology open-platform architecture that is future-proof, scalable, and extensible.
OPC-UA and IIoT
OPC UA is a service-oriented architecture (SOA) framework that can be developed to support a wide range of platforms, from embedded microcontrollers to cloud infrastructure. Since it is platform-independent and adaptable from sensor to cloud, it can be integrated into devices, making it a complete solution for IoT-based applications. This also enables Internet of Things (IoT) players to model data based on domain-specific products. OPC UA is the preferable protocol for the IIoT as it has all of the features that it should have. It is an industrial standard for data packing from the edge (machines in industrial units, PLCs, Pneumatic controls, etc.).
OPC and IoT both function behind the scene for consumers, with the business objectives including insights into Productivity, OEE, and Quality, as well as a platform that allows Data-driven decisions, making it easier to develop IIoT technology-based OPC UA solutions. OPC UA allows distant devices to be easily connected to IoT in the cloud or at the edge, enabling device diagnostics, asset management, and monitoring, reporting, and other applications. It ensures security by encrypting data, authenticating users, and auditing operations. It develops on OPC Classic by providing on-demand capabilities, the ability to identify servers and other devices on a network, and an address-space architecture designed to support more sophisticated data structures.
OPC – UA towards an Industrial Automation:
Prior to the development of OPC, each OEM manufacturer had applications that used its own drivers and kept data in complete data paths. This created a slew of issues for manufacturers because each vendor generated their own data, which they couldn’t use to report generation. For report creation, they had to develop unique solutions from these various vendors. So because data was locked in an exclusive format, only a few combinations were possible. Data was stored in various PLC models, HMIs, CNC machines, ERPs, and so on. Furthermore, anytime a new system was added, the plants overlooked the problem of modifying management. Rather than developing a new product to regulate technology with no exclusive format and to facilitate widespread connectivity, OPC was established as a solution to these concerns. A namespace is established when an OPC server describes a group of variables within a directory tree-like hierarchy. Each variable has various types of data, such as an integer, a Boolean value, a real value, a string, and a default value. A TCP-based binary protocol is used to connect one or more OPC clients to the OPC server.
The OPC Unified Architecture (UA) has been described and is being tested and implemented as part of the program’s Early Adopters. It may be implemented in Java, Microsoft.NET, or C, removing the necessity for previous OPC versions to need a Microsoft-Windows-based platform. To provide higher level MES and ERP support, UA combines the capabilities of current OPC interfaces with new technologies such as XML and Web Services.
The Platform Industry 4.0 has thoroughly examined OPC UA and validated it as a key technology for implementing the ‘Communication Layer’ of the ‘Reference Architecture Model Industry 4.0.’ (RAMI4.0). The OPC UA protocol is standardised as part of the IEC 62541 series. It should be noted that the OPC UA specification is the most recent one that is not based on Microsoft COM technology and so enables cross-platform compatibility.
The OPC UA paradigm, as illustrated in the preceding figure, describes how clients access information on the server. The OPC UA layer includes a detailed description language as well as the communication services required for information models. These systems are distinguished by their size, performance, platforms, and functional features such as Client-Server and PubSub.
OPC UA can be integrated into existing Industrial Ethernet networks and run on existing PROFINET infrastructure without compromising quality. OPC UA’s goal is to extend interoperability to device and enterprise applications, and it recently introduced publish/subscribe to the original client/server communications infrastructure. The specification also seeks to eliminate the need for a standalone Windows PC by allowing a server to be integrated with an edge device.
Standards of OPC used in Industrial automation systems
The goal was to abstract the communication protocols of PLCs, which are small, special-purpose computers used extensively in industrial automation. By abstracting these various protocols, a standardised interface that served as a sort of middleman converting read/write requests between HMI software that employees use to control machines via PLCs and SCADA (supervisory control and data acquisition), a popular computer architecture for industrial process control, was formed.
OPC technology includes a number of standards (OPC DA, OPC HAD, OPC AE, OPC Batch, OPC DX, OPC Security, OPC XML-DA, OPC Complex Data, OPC Commands, and OPC UA) that describe a specific set of functionalities. The most prevalent standard is the OPC DA (Data Access), which defines a collection of functions for real-time data exchange with PLCs, DCSs, HMIs, CNCs, and other devices. The OPC HDA (Historical Data Retrieve) module allows you to access previously recorded data and history. Another standard, OPC AE (Alarms & Situations), provides on-demand notification features for a variety of events, including emergencies, operator actions, information messages, and others. OPC Batch controls the technical process at the step and recipe level. The OPC DX (Data interchange) function manages data exchange between OPC servers via an Ethernet network. The primary goal of this standard is to build data exchange gateways between devices and applications from various vendors. The functions of arranging client access permissions to OPC server data are defined by OPC Security. The OPC XML-DA (XML-Data Access) standard is a versatile, rule-based format for transferring data through XML, SOAP, and HTTP. OPC Complex Data is a collection of supplementary OPC DA and XML-DA specifications that enable servers to communicate with complex data types such as binary structures and XML documents. The OPC Commands are a collection of programming interfaces that enable OPC clients and servers to identify, send, and control commands that are performed in a controller or I/O module. OPC DA is the most widely used standard, however it has a significant drawback. It was based on then-modern Windows technologies such as OLE, ActiveX, and COM/DCOM at the time of its development, but the industry has changed and other operating systems and technologies have gained prominence.
Use Cases OPC
Seamless Data Exchange via OPC-UA
Intelligence is transferring from supervisory control systems to local components as the industry moves toward horizontal and vertical integration. This growth is creating an increase in the need for communication, for which the open OPC-UA standard, which can also be used for embedded devices, is an appropriate solution. Embedded OPC-UA is a server gateway that connects the control and IT worlds by providing access to process, manufacturing, and quality data in a range of different controller types.
Water Management with OPC UA Enabled Smart Devices
Decentralized, self-contained embedded controllers can work together to build an intelligent network for controlling potable water and waste water plants. OPC UA is the appropriate solution for establishing secure and standardised M2M communication at these plants. OPC UA is utilised between plants for M2M communication or IoT Technology for the intelligent networking of decentralized, autonomously functioning, and very small embedded controllers. Because the controller has an OPC UA server, these objects are instantly exposed to the outside world as sophisticated data structures enabling semantic interoperability. As a result, decentralized intelligence emerges, capable of making independent decisions and transmitting information to neighboring systems.
Many OPC tool kits, software, and companies’ modules are available to execute design, development, and also projects on Open Platform Communication. Newark has partnered with several suppliers catering to an array of industrial OPC components such as OPC, opc-toolkit, process-controllers Accessories, converters-interfaces, software-starter-kits, PLC, and Industrial computing.