More Efficient Wire Processing
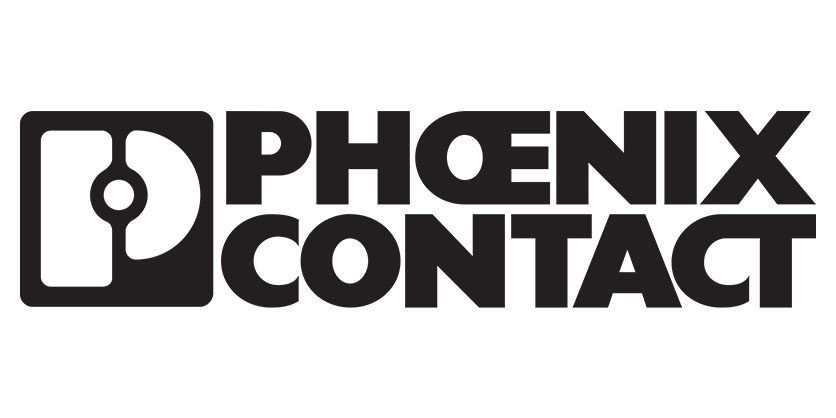
July 19, 2023
By Katharina Faes, Director of Product Marketing Business Unit Marking and Identification, and Jens Frischemeier, Manager of Product Marketing Business Unit Industrial Cabinet Solutions, Phoenix Contact GmbH & Co. KG, Blomberg, Germany; and Maria Schierscher, Associate Product Marketing Manager for Industrial Tools, Phoenix Contact USA
Optimized Processes and Coordinated System Solutions for Greater Efficiency in Wire Processing
Control cabinet builders face many challenges: international competition, the shortage of skilled workers, and financial considerations such as increasing labor and material costs. While panel shops have little influence over these external challenges, they can find ways to streamline in-house processes and structures.
Due to the sheer number and variety of manual activities performed, the process chain in control cabinet building offers significant potential for efficiency gains, both in engineering and production. Panel builders can achieve more efficient and economical processes by implementing more coordinated systems. (Figure 1)
Identifying time-consuming process steps
The continuity of the process chain – from engineering to the assembled and wired control cabinet – is vital for efficiency and competitiveness in control cabinet building. There is considerable untapped potential, especially in wire preparation, identification, and wiring. These time-consuming steps account for up to two-thirds of the control cabinet builder’s total working time. Production runs involve many manual steps. The best way to improve cost-effectiveness and flexibility is to optimize the use of hand tools, automatic tools, and manual and automated marking systems.
Automating and bundling core processes
An automatic, mobile wire processing station can often replace hand crimping tools – even for small to medium quantities. Automatic cutting devices, such as the CUTFOX 10, can cut wires precisely and with repeat accuracy at high speed. Phoenix Contact’s CF 500 can crimp a multitude of connectors including up to 1/0 ferrules. Machines with interchangeable dies for different types of contact enable more flexibility in production.
Another way to optimize productivity is to bundle the stripping and crimping processes. Depending on the production conditions, these stripping and crimping devices, such as the CF 1000 and CF 3000 from Phoenix Contact, can reduce time and costs by up to 70 percent. The technician inserts the wire into the device, automatically triggering the process. The device strips the wire, then attaches and crimps the ferrule in just a few seconds.
When it comes to identifying individual wires, it is important to consider the markers’ physical and tactile properties, along with the chemical resistance requirements. Numerous marking solutions are available to meet all cross-section ranges and mounting situations. Marking technology includes conventional thermal transfer printing, versatile UV LED printing, or highly durable direct laser marking.
Marking, separating markers by hand, and finally mounting them on wires takes a lot of time. There is considerable potential for increasing efficiency here. A modular system, like the THERMOMARK E SERIES from Phoenix Contact, can automate and combine the printing and application of different marking materials into just a single step. This automated process can be up to 60 percent faster than traditional industrial identification. (Figure 2)
The automated printing and applying process enables intuitive handling and ensures a consistently high level of marking quality. In turn, this results in higher efficiency over the entire working day. The automated system consists of three applicators, which provide various marking solutions for wire and cable identification. The applicators can connect to a standard thermal transfer roll printer that can print all kinds of marking materials in roll format – such as creating labels for equipment identification. This eliminates the need for an additional marking device.
Efficiency and ergonomics
A worker assistance system, such as the Phoenix Contact clipx WIRE assist, offers a scalable approach to improving efficiency and ergonomics. A software-supported system guides the user through the entire process of semi-automated wire production. At the same time, the technician can directly control the individual automatic tools and printers. The necessary information for further processing and wiring is visually enhanced and automatically displayed on the monitor in an easy-to-follow format. (Figure 3)
This system is built around a height-adjustable workbench. The height adjustment feature is not just a one-off adjustment to the physical height of the worker or the activity being performed. It also satisfies another key ergonomic requirement: the ability to switch between sitting and standing while working. The compact worker assistance system is mounted on four industrial-grade castors with brakes, making it mobile. This means it can be used where the work needs to be performed, reducing or eliminating unnecessary legwork.
With the workbench’s modular design, the worker can freely arrange it to fit his or her individual needs. Automatic tools and marking devices do not have to be positioned on the surface of the worktop bench, as they can be attached directly to the basic framework instead. The devices can be positioned flexibly in terms of height and orientation, and their positioning can be tailored to personal needs. This solution meets all the requirements for a comfortable and fatigue-proof workstation. Guides are attached to the support arms and columns to hold additional accessories, such as wire routing systems.
Nothing works without data and software
In addition to this high level of flexibility, the worker assistance system can boost productivity even more when paired with compatible software. The intuitive software controls the devices and guides the user through the entire process of wire preparation. This significantly reduces the manual effort involved and minimizes errors. The graphical user interface features touch capability and boasts a clear and intuitive design.
Comprehensive data and the consistent flow of data without system discontinuities save both time and money during project implementation. The necessary wiring information for the automated completion of the process steps can then be exported from CAE programs and imported into the software. (Figure 4) To maintain an overview, especially in extensive and multifaceted projects, and to ensure that wires are processed as effectively as possible, select a software with filter and sort functions. For example, wires of the same type and size can be produced directly after one another, eliminating unnecessary changes in the material.
Conclusion
Panel-building jobs can range from a fully equipped worker assistance system with automated marking to meet high demands to a typical workbench with hand tools, automatic tools, and marking systems. But whether the job is simple or complex, it is important to tailor wire processing to the individual production environment and its specific requirements.
Flexible worker assistance and software solutions can streamline projects and reduce both time and costs. The intuitive software guides the user step by step through the entire process. From wire processing to wiring, this ensures a smooth and reliable production process.

Learn more at www.phoenixcontact.com/clipxwireassisst or https://ext.phoenixcontact.com/en/smartproduction/index.html