The Function Of Control Panels In The Oil And Gas Industry
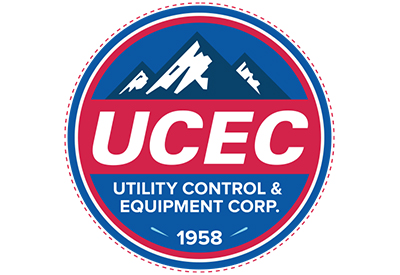
October 20, 2021
By Garrod Massey
Control panels for the oil and gas industry can be grouped into the three main process stages oil and gas go through to transform from a resource in the ground to a commodity. These are upstream, midstream and downstream. Control panels in each of these stages help execute very different things from drilling holes to, ensuring accurate transportation or refining the product.
UPSTREAM CONTROL PANELS FOR OIL & GAS
During the upstream stage, oil and gas companies survey land to assess where the resource is, drill holes in the most strategic areas and, of course, pull the resource out of the land. Finely calibrated machinery is used to accomplish the last two steps of this process and control panels are used to control these machines.
Since these machines need to be in the field, upstream panels are generally pretty small and very, very durable. They are used for monitoring pressure, flow, temperature, valve position as well as emergency shutdown (ESD) operations in the production/drilling phase. These panels are often referred to as an “RTU Panel” (Remote Terminal Unit). Due to their generally small stature, they are usually optioned with solar power as a backup.
Given the remoteness of the areas these RTU Panels are positioned in, they primarily collect, analyze, and send data over licensed radio waves to the master supervisory control and data acquisition (SCADA) system.
Like a majority of other oil and gas operations, these panels are located in areas that have extreme temperature fluctuations, various wet and dry corrosive properties (including salt water if they’re commissioned for offshore operations), as well as high concentrations of hydrogen sulphide, H2S, a poisonous and, highly ignitable gas. These panels have to be built to hazardous location standards to prevent the electrical equipment inside from igniting the concentrations of gas. H2S is also highly corrosive. If it isn’t properly removed from the gas, it can eat through tooling and pipelines. Most of our panels destined for upstream oil and gas work are made with a high grade of stainless steel categorized as 316 stainless. Our typical stainless steel panels are considered 304, but H2S gas would still quickly corrode those panels.
To achieve maximum portability, most upstream control panels are mounted on a skid along with other electrical and mechanical controls. This allows the operators to move all of their main controls from one area to another as a single unit. There are a lot of finely tuned instruments housed on a skid, but with routine maintenance and part replacement, these skids typically last anywhere between 5-10 years. More commonly, the skid will fall out of compliance with constantly evolving electrical codes forcing it to be decommissioned or modified to remain compliant.
MIDSTREAM CONTROL PANELS FOR OIL & GAS
Midstream Control Panels share a lot of the same elements of the upstream panels, except these panels control the processing, transportation and storage of the oil or gas produced during the upstream process. They monitor and act upon the same types of data and reside in similar hazardous locations.
Long and short term storage of crude oil and gas product is very common. The oil and gas industry is very sensitive to the market. As the market fluctuates, some of the larger companies may decide to keep pumping the oil, but wait to process it until the market offers a more favorable rate for their refined product. Refined oil and gas has a shelf life that the companies can delay starting the clock on by storing the product in tank farms. Tank farms are large tracts of land with bulk storage tanks for unrefined oil and gas. Proper storage of these resources is critical and control panels can be used to help monitor different conditions within the tank until the oil or gas is ready for transport to begin the downstream stage.
Once transportation of the resource is needed, the oil and gas gets transported by a pipeline, rail car, or a tanker truck. On a pipeline, panels are used to monitor and report a lot of the same elements we’ve seen elsewhere in the process: flow, temperature, pressure, etc.
If the resource is being transported by rail or tanker truck, a lease automatic custody panel, or a LACT panel is involved in getting the stored oil onto a truck. Oftentimes, the company that drills the oil or gas, the company that stores it, and the company that refines it aren’t all the same company. One crucial component on a LACT skid, where the control panel is housed, is a flow meter and flow meter proof point. This will tell the operators from both companies the exact amount of oil or gas flowing into a truck so there can be no disagreement on volume. Other processes carried out by LACT skids often include gravity and sediment measurements, giving the transport company an accurate read on usable product vs waste.
The railcar and truck may be equipped with accessory panels that monitor the resource while in transit and can let the operators know the weight of the product they’re hauling.
OIL & GAS DOWNSTREAM CONTROL PANELS
Downstream Panels come in many shapes and sizes and are vast. These panels control everything involved with refining the oil and gas for Commercial, Industrial and Consumer use.. Since refineries have hazardous and non-hazardous locations, panels can have a wide variety of parts and capabilities dependent on location. Refineries often have Master Control Rooms housing consolettes, human machine interfaces, and lots of computing power.
One common component of downstream panels are their safety precautions. Hazardous locations are defined in this industry as anywhere that could or does have an ignitable concentration of gas in the air. All equipment in these areas are required to not have open flames, sparking, arcing, or surface temperatures outside of a specified range to avoid auto-ignition temperature.
There are two different classes of location that define the environments downstream control panels operate in. C1D2 class one, division two is the safer of these two environments. Under normal circumstances, there shouldn’t be any ignitable gases or vapors. One way to make these panels safe for a C1D2 environment is to equip them with purge units.
A purge unit creates an environment inside the panel that makes it impossible for an outside ignition source to get in, therefore when arcing and sparking occurs, there won’t be an ignition source. This is accomplished with an air compressor that feeds around 120PSI of compressed air or inert gas into the purge unit, which pumps a specific amount of air into the cabinet creating constant positive pressure. The air or inert gas pumped into the panel is measure in inches of water (inH2O). The amount of pressure considered to be the “SAFE ZONE” is between .15 and .35 inches of water. Anything less and hazardous gas could seep into the panel. Anything more and the enclosure runs the risk of being over-pressured and warping. A lot of companies don’t want to purchase an air compressor nor do they want the added cost of operating one constantly. The other option for C1D2 panels is to create them all with non-incendive components. Most of these components are solid state, meaning contacts are switched electronically with no moving parts. However, some of these components still produce sparks, yet they are manufactured in a way that would contain the spark within the unit itself. This method is commonly referred to as sealed or hermetically-sealed.
C1D1 environments are defined as environments where, under normal circumstances, there is an ignitable amount of gas or vapor. Panels equipped with purge units are an accepted option for C1D1 environments as well, however these panels must have automatic shutdown feature if pressure are lost or get below the safe zone. The other option is to build explosion proof panels. These control panels are built to contain an explosion without letting any flame or increase in temperature to occur outside the box. These panels are very thick and incredibly heavy. A small 12” x 12” box can weigh between 50-80 pounds. They are made with a vast amount of very thick bolts capable of keeping the panel together if an explosion were to occur inside. When adjusting these panels, it can take 15 minutes just to pull the bolts off.
It’s easy to assume oil and gas is the most hazardous industry due to the components involved. But as far as hazardous locations go, environments that store grain or have a lot of flammable dust are actually more dangerous. The fibers in the air often prove much more ignitable than the gases produced from refining oil and gas.
The oil and gas industry has many machines and systems to pull the resource out of the ground, store and transport it, and refine it. A variety of custom control panels are used in every stage of this process to aid operators in monitoring the processes, collecting data and controlling various components.
https://www.ucec.com/news/functionofcontrolpanelsforoilandgas