SCHURTER: Projected Capacitive Input System (PCI) – Multitouch Systems for Industrial Applications
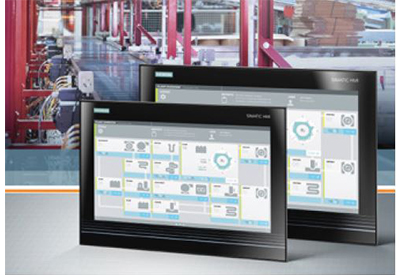
November 19, 2021
Multitouch technology is the focus of many new developments in the human machine interface (HMI) and medical fields. Based on projected capacitive technology, multitouch panels have undergone further development into an industry-compatible input system. The high electromagnetic compatibility (EMC) interference immunity requirements, adequate water tolerance and the glove operation option qualify it for industrial applications.
Projected-capacitive input systems with a sealed glass panel without dirt-collecting edges are easy to clean and are scratch-proof, abrasion- and chemical-resistant. They therefore allow multi-purpose use in industrial automation, machine construction and medical technology. The sensor positions are protected behind the glass panel and, for that reason, are not affected by mechanical stress. Multitouch allows more intuitive, faster and safer operation of machines, equipment and systems. New visualization and operating concepts have allowed a major leap in multitouch input system design innovation.
Configuration and Function
Projected-capacitive touch sensors consist of at least two electrically separate sensor surfaces, glass or polyester films that are coated with conductive, highly transparent indium tin oxide (ITO). Using an etching or laser process, the ITO surfaces are segmented into many small individual fields, mapped as x/y intersections into rows and columns. The design potentials of these sensor fields are wide-ranging and follow the different guidelines of the PCAP basic chip manufacturers.
The structures are outside the viewing area with printed or laser-etched silver conductive ink circuitry contacted and conducting to the connector contacts. Film-based sensors are laminated so they are highly transparent and electrically insulating. As a result, a matrix network of individually addressable sensors with quiescent reference capacitances is generated over the entire active surface. With the approach of a finger its position is detected by the change in the capacitance of the individual sensor. Through the interpolation of the adjacent sensor capacitances the controller can calculate the exact positions of the activations and convert them into the corresponding x/y-coordinates. The matrix arrangement of the individual capacitive sensors requires no calibration. As a result, industry-compatible projected capacitive multitouch systems always work with position precision even under harsh environmental conditions.
The electronic evaluation of the touch detection works using two principal methods. In both types a capacitive sensor field is projected through non-conductive media such as glass. The change in the self-capacitance or the mutual capacitance of the sensors is determined in the process. In the selfcapacitance method the increased charge flow of the x- and y-sensors due to the approach is determined at the ground level. The activation position is the point where the sensors display an increased charge flow. The mutual capacitance method detects a change in the sensor matrix capacitance due to a parallel coupling of the finger at the intersections. Both evaluation methods have advantages and disadvantages. The electronics of an industrycompatible PCI touch controller ideally uses a combination of both methods.
Industrial requirement: interference immunity, water tolerance and glove operation
One of the most important factors for achieving industry-compatibility is immunity to EMC interferences with the system. During EMC radiation the touch panel must be operated with at least two actuators. That is the only way absolute EMC immunity can be qualified.
To achieve an EMC immune multitouch panel, two main sources of interference are considered. The first sources of interference behind the touch panel are integrated displays and switch mode power supplies. The EMC standard according to IEC- 61000-4-3 refers to these interferences. Furthermore, the IEC- 61000-4-6 EMC standard defines the gridlinked coupling of voltage peaks and frequencies. Elimination of interference signals so that the multitouch panel works with position precision without causing a deviation of the touch function and no false activations is the prerequisite for the achieving EMC class A conformity.
This EMC immunity is achieved with optimized AD converters, integrated RC filters, enhanced drive voltages and complex algorithms, e.g., the frequency-hopping technique. In addition, an enhanced signal-to-noise ratio is obtained with a sensor design adapted perfectly to the electronics.
This optimization of interference-immune sensor sensitivity allows finger activation through several layers of medical gloves and thicker leather construction gloves. Water must never lead to false activations of the multitouch panel. An additional requirement in the medical field particularly is resistance to saline solution. The possibility of achieving complete water resistance consists in the selection of optimal controllers and their measurement methodology. Thus PCI input systems are possible, even for use under running water with simultaneous detection of the finger activation. Absolute industry-compatibility however will only be achieved if all requirements, i.e., EMC interference immunity, water tolerance and glove operability can be guaranteed with a single software setting. In any event, conventional, standard design PCAP controllers and sensors from the consumer sector do not satisfy these high industry requirements.
System integration: the multitouch screen becomes the multitouch panel
At SCHURTER glass-based sensors up to 24” are liquid bonded to the front glasses with a fully automated process in the clean room. A specially designed system determines the glass thicknesses of the sensors and front glasses in the first step, then calculates the necessary amount of adhesive and bonds the glasses at a defined, fixed distance. Highly transparent UV adhesives that can also cure with air humidity are used exclusively. Reliable bonding can thus be achieved, even in areas where UV light cannot penetrate to do the curing.
Film-based sensors are also applied behind the printed front glasses with highly transparent adhesives using automated turntable laminators in the clean room. In the second step, the color phase in the window area requires storage in the thermostat controlled autoclaves in overpressure conditions. As a result, the resulting minor air entrapment of the highly transparent adhesive after the lamination is completely eliminated at the printing stage. The customary finger gestures of the multitouch user are subject to very high static friction during the movement of the fingers across the glass surface. A selected anti-glare or anti-smudge surface reduces this static fraction considerably and allows a pleasant gliding of the fingers over the multitouch panel.
The anti-glare glass surface with the etched surface structure however also causes inconvenient overlappings of the display pixels. To avoid these unwanted effects, the front glasses are qualified and selected with a sparkle measuring device so they optically fit the display. The printing of the glasses on the back side is done by a fully automated screen printing system in the clean room. In this printing line the glasses run through a special pretreatment process to ensure optimal adhesion of the UV colors.
A special adhesion technology of the front glasses in the carrier plate or in a housing allows very high extrusion forces. The inlay in a deep milling groove creates mechanical protection of the glass edges. The circumferential gap between glass and carrier frame or housing is enclosed in an automated process. Against ingress of moisture and dirt after IP 67K protection thus is possible over the complete front unit. The qualified sealing material is chemically resistant, with temperature stability and protects the color printing on the back side of the front glasses against aggressive media that can affect the touch panel during use.
The back side assembly of the display with dust seals and electronics also takes place in the clean room. For high optical requirements the air gap between display and back side of the sensor is cast with liquid UV material. This optical bonding causes an increase in contrast and thus improved legibility. Due to this liquid bonding light refractions inside the panel are reduced. In addition, the touch panel with a bonded display is more resistant to mechanical stresses.
For HMI input systems frequently required function keys are provided outside the active surface of the PCI panel by programmable capacitive individual keys behind the front glass. Flat, point-like illumination of symbols and touch point labels as well as status LEDs are integrated behind the front glass. “Fading effect” printed labels are detectable only with back-side illumination. Additional sliders and wheels can also be implemented in or on the glass as a haptic finger guide for the users.
Multitouch-capable PCI panels increase ergonomics and allow intuitive operating concepts for the industrial sector.
In automation the finger gesture is used for example when scrolling through settings or in the search within production documentation. Other options include navigating by swiping in overviews and enlarging process pictures and characteristic curves with the zoom-in gesture. With the two-handed operation, the user can select a parameter with one hand while adjusting a change in level with the other.
With Multitouch complex machine- and plant-visualizations therefore can be reviewed an operated much more easily which increases system safety.